液压阀的制造,首先是按设计图样、工艺文件和技术要求精心加工阀芯、阀体等零件,其次是择优选购配套件(如电气–机械转换器等) ;最后精心装配,通过按相关标准试验得到优质产品。由液压阀的组成零件很多,不便逐一论述,故本节仅就液压阀中的阀体(壳体)、阀芯、阀套等主要零件的材料、加工和装配工艺进行简要介绍,如读者欲详细了解相关内容,可参阅相关专著或手册。下面让我们一起来了解下液压阀制造工艺中的主要构件材料。
1、 阀体(壳体)的材料
(1) 以液压油为工作介质的普通液压阀中阀体的材料绝大多数为灰口铸铁(如HT250. HT300等)或球铸铁(如QT400-15, QT500-3等) ,少部分采用合金铸铁和蠕墨铸铁,油道多为铸造成形。液压件铸件毛还要有足够的强度、韧性、弹性模量等机械性能及致密性,以便承受较高的工作压力;铸造毛还要有精确的定位基准、准确光整的外形及光滑的铸造内流道,以便满足数控机床、加工中心等加工手段的要求并减少系统压力损失;铸件内腔应清洁,无任何残砂、锈蚀、氧化皮和其他杂物.以便提高阀及系统工作的可靠性。
(2) 伺服阀的阀体常称为壳体,其使用的材料种类较多.一般多采用不锈钢1Cr18Ni9Ti,9Cr18, Cr17Ni2制造。也有用铝合金LDIO,ZL105制造的。近年来逐步采用沉淀硬化不锈钢OCr17Ni4Cu4Nb制造。这种钢具有一般不锈钢的抗腐蚀特性,同时又可通过沉淀硬化提高其强度,是一种高强度不锈钢,其抗腐蚀性近似于奥氏体不锈钢1Cr18Ni9Ti.抗拉强度优于30CrMnsi.
(3) 以水为工作介质的水压阀阀体的材料可选用LD5, LDIO等锻铝,加工后对铝件表面进行阳极氧化处理,也可采用1Cr18Ni9Ti等奥氏体不锈钢材料。
(1)油压阀中阀芯、阀套等精密零件一股选用45钢、40Cr,Cr12MoV, 12CrNi3A、 18CrMnTi, 18CrNiWA及GCr15等高级工具钢、高合金结构钢、优质钢及轴承钢等材料。要求材料具有良好的耐磨性、线胀系数和变形量小等优点。为了提高阀芯的耐磨性,必须使材料表面达到一定的硬度(一般要求≥58HRC)。因而.针对不同的材料可选用淬火、渗碳、渗氮等不同的热处理手段。(2)水压阀中阀芯的材料除了要求能达到较高的硬度外,还应有良好的耐淡水或海水腐蚀性能。虽然奥氏体不锈钢的耐腐蚀性能较好,但难以通过热处理提高材料的表面硬度,因此不适宜作为阀芯材料。一般可选用2Cr13/ ICrl7Ni等马氏体不锈钢、0Cr17Ni4Cu4Nb等沉淀硬化不锈钢或工程陶瓷作为水压阀阀芯的材料。其中马氏体不锈钢只能用于淡水. 0Cr17Ni4Cu4Nb是一种高强度不锈钢,抗腐蚀性能接近1Cr18Ni9Ti奥氏体不锈钢。该不锈钢加工时一般先进行固溶处理,在精密加工前进行沉淀强化处理(当时效温度在420℃,保温10h以上时, 可获得最高硬度)
水压阀中阀套的材料首先应具有良好的耐腐蚀、磨损性能。此外阀套与阀芯材料的合理搭配也十分重要,应防止阀套与阀芯材料发生黏着磨损、腐蚀磨损等,以提高水压阀的寿命和工作可靠性。阀套一般可选用耐腐蚀性好的QA19-4青铜或高分子材料。其中高分子材料应具有强度高、耐磨性好、线胀系数小、吸水率低、加工性能好等特点。
液压阀的组成零件很多,不便逐一论述,故本节仅就液压阀中的阀体(壳体) :阀芯、阀套等主要零件的材料、加工和装配工艺进行简要介绍,如读者欲详细了解相关内容,可参阅相关专著或手册。
下面让我们一起来了解下液压阀制造工艺中的主要构件加工工艺:
液压阀要求阀芯在阀体孔内移动灵活、工作可靠,泄漏小且寿命长。在油压阀中,通常各种滑阀的配合间隙为0.00 5-0.035mm.配合间隙公差为0.005-0.015mm,其圆度和圆柱度的允差一般为0.002-0.008 mm。对于台阶式阀芯和阀孔,各圆柱面的同轴度允差为0.005-0.01mm。对干平板阀阀芯与阀座的平面度误差应不大于0.0003mm。阀芯与阀孔的配合表面.一般要求表面粗糙度Ra值为0.1-0. 2um。考虑到孔的加工比外圆困难。一般规定阀芯外圆的表面粗糙度Ra值为0. 1um,阀孔内圆表面的Ra值为0.2um。可见,对阀芯和阀孔的形状精度、位置精度及其表面粗糙度都有较严格的要求。若对于水压阀,则上述各项要求会更高。为达到所要求的加工精度,阀芯的加工在进行车、铣、磨后,最后还需光整加工。阀芯外圆常用的光整加工方法有研磨和高光洁度磨削。阀孔的加工一般在进行钻孔、扩孔、铰孔、镂孔、磨孔后,再光整加工。孔常用的光整加工方法有绗磨、研磨和挤压等。
目前,国内主要液压元件厂对液压阀零件的加工大多数采用数控机床/加工中心和高效专机相结合的工艺装备,辅助工序则采用通用机床。
不同类型、品种液压阀的阀体加工工艺有所不同。例如普通液压阀中的电液换向阀的阀体,其主孔与阀芯的配合间隙很小,要求在高压下阀芯在主孔内换问灵活,同时又要求阀的内泄漏量不超过规定值;各连接面不得有外泄漏,所以,阅体的主孔及其他各面的加工中,应达到很高的尺寸精度、形状精度和较低的表面粗精度。
阀体内各轴向尺寸也必须控制在其公差范围内,以确保阀芯各台阶尺寸配合位置正确,阀体主要尺寸及精度要求见图2-37,采用卧式加工中心对电液换向阀体的加工工艺流程大致为:粗铣各平面惚主孔两端加工阀体底面及底面上各孔–加工阀体两端面、顶面及两端面名孔、加工主孔及孔内各槽节距–去刺、清洗一主孔珩磨等。
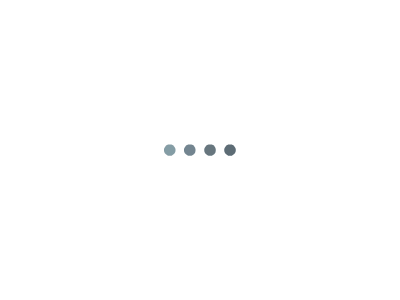
伺服阀的壳体常见结构如图2-38所示。孔D与阀套配合,配合间隙为0.001-0.003mm,表面粗糙度为Ra0.2um,圆柱度为0.0005mm,孔d和喷嘴体成过盈配合,过盈量为0.005-0.007mm,表面粗糙度为Ra0.4um,圆柱度为0.0005mm,与上端面的平行度为0.03mm。此外还有油滤孔,其两端堵头多采用密封圈密封结构。图中斜孔的精度比前述两孔低,表面粗糙度为Ra1.6um,精度等级大多为IT7-IT9,长径比在8-12.壳体中有较多的油路连接小孔,其直径一般为0-1.5mm。并多为斜孔,长径比在30以内。
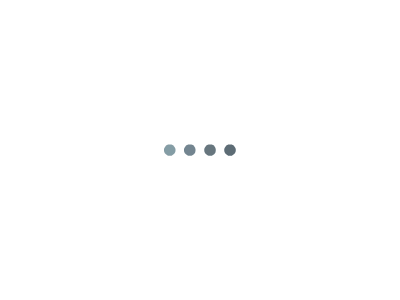
底面的安装孔及通油孔大部分已标准化,其中通油孔的端面密封槽,有内墙结构形仪式和无内墙结构形式,尺寸精度要求一般为1 -10级, 粗糙度为Ra1.6um,为了便于加工,也可以把壳体结构设计成组合式的,即分成几个部分加工,然后组合成一体。这种结构加工方便,也易于保证加工质量,但阀体的强度刚度和密封性较差。伺服阀的阀体主要加工工序见表2-17.
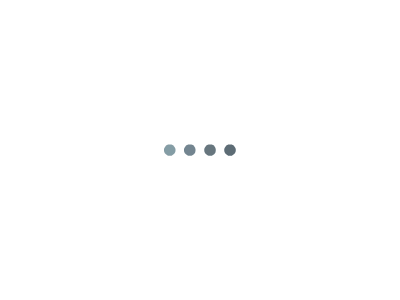
(1)普通液压阀的阀芯有滑阀和提升阀(锥阀和球阀)之分、故阀芯结构及其加工工艺有很大不同。现以方向控制阀的滑阀芯为例,对其加工过程说明如下:方向控制阀为滑阀阀芯装在阀体主孔内,其一般配合间隙为0.01mm左右。它在阀体主孔内可以轴向自由滑动,不得有阻滞。这就要求阀芯应有较高的尺寸精度和圆柱度。较低的表面粗糙度,以保证阀芯换向时灵敏度高而泄漏量小。阀芯的主要结构尺寸及其技术要求如图2-3所示、主要的制造工艺过程为车削各外圆及其端面。
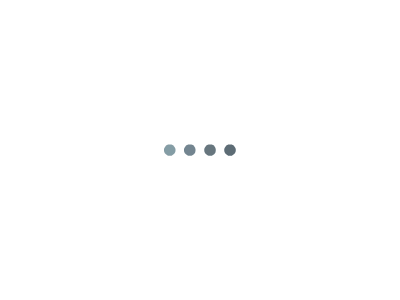
(2)电液伺服阀中阀芯和阀套称为滑阀偶件,靠两者的轴向相对运动改变节流孔面积,对液流进行控制。滑阀偶件的制造精度,特别是阀芯和阀套的配合间隙/节流工作边的尺寸和形状以及他们的相互配合精度直接影响到伺服阀的多项性能,也会影响伺服阀的使用寿命。伺服阀的滑阀偶件要比普通液压阀的技术要求高,见表2-18
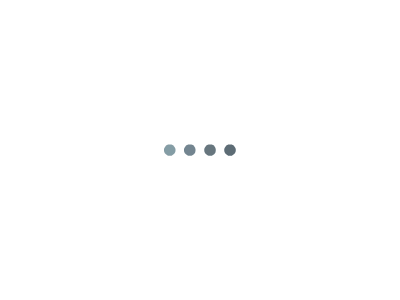
图2-40表示为四通断续节流窗口阀套和全周边(内环槽)节流窗口阀套。其内孔与阀芯配套,保证间隙为0.001mm-0.003mm,其外圆与壳体配套,保证间隙为0.001mm-0.003mm,表面H与内孔B相交处去毛刺保留锐边(R不大于0.005mm)。图2-40中16个矩形窗口宽度b相差不大于0.01mm,同一个H面上4个矩形孔工作边的位置度公差(通常称为共面度)为0.002mm。
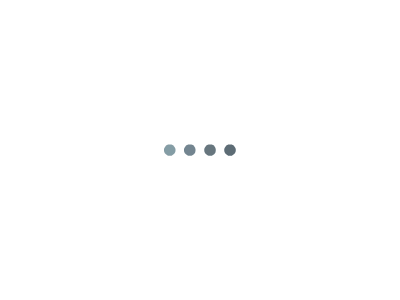
阀套内孔直径一般为8-19mm,孔深比L/D为7-12。阀套外圆与壳体一般采用间隙密封,也有采用过盈量很小(过盈量为0.002mm)的过盈配合,或者采用橡胶圈密封。采用橡胶密封时可适当加大配合间隙,但对胶圈沟槽的制造有严格的尺寸和粗糙度要求。这两种常见阀套的典型加工工艺过程见图2-41.
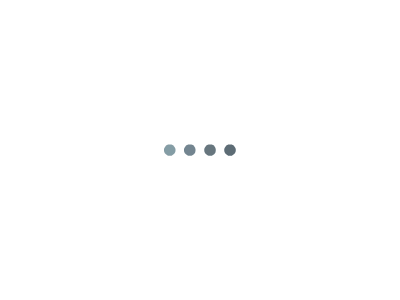
典型阀芯的结构简图如图2-42所示。
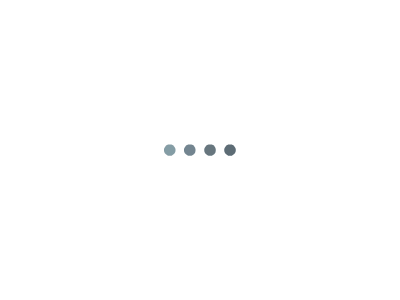
其外圆d与阀套内孔配磨,保证间隙0.001mm-0.003mm,四个台肩轴向工作边的位置尺寸ABC与阀套上相应的节流工作边配磨,保证重叠量要求。反馈槽两端与反馈杆小球配磨,保证间隙0-0.0015mm,外圆和槽的形状位置精度要求也很高,故阀芯的加工难度较大。阀芯的典型加工工艺过程见图2-43:
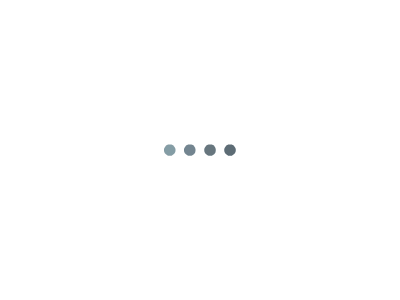
原文始发于微信公众号(伺服阀及电液伺服系统):液压元件制造
本文来自伺服阀及电液伺服系统,本文观点不代表iHydrostatics静液压立场。