第一作者简介:李少年(1977-),男,安徽泗县人,副教授,硕士,主要从事流体传动与流体测控方面的科研与教学工作,就职于兰州理工大学能源与动力工程学院。
基金项目:国家自然科学基金项目(51565026);甘肃省高等学校科研项目(2015A-044)
摘 要:轴向柱塞泵结构相对紧凑复杂,其可靠性与寿命的长短主要取决于三大摩擦副,缸体-配流盘摩擦副、缸体-柱塞摩擦副和斜盘-滑靴摩擦副,同时与该三对摩擦副的热处理工艺、加工精度以及配对材料相关,其中选用合理摩擦副材料最为重要。该文开展轴向柱塞泵缸体-配流盘摩擦副的磨损实验研究,选用缸体材料为烧结铜、ZQAL9-4,选用配流盘材料为25Cr3MoAl、18CrMnTi以及38CrMoAl,组成三对摩擦副,使用立式万能摩擦磨损试验机进行实验。结果发现以烧结铜、38CrMoAl为配对材料的摩擦副摩擦系数较低,且具有最小的磨损量,可以推荐作为轴向柱塞泵配流副材料选用,实验结果为解决配流盘磨损问题提供一定的参考性依据。
关键词:轴向柱塞泵;配流盘;摩擦副;摩擦系数;磨损量
液压泵主要包括齿轮泵、叶片泵和柱塞泵,柱塞泵具有效率高、寿命长、可靠性高等优点,被广泛应用于工程机械、船舶、航空航天等领域。容积式液压泵正常工作须具备两个基本条件,第一,具有密闭的工作容腔;第二,工作容腔容积可变并具有配流机构。轴向柱塞泵靠柱塞在缸体中做往复运动,从而改变密闭容积,实现油液的吸排过程,其缸体相对配流盘做高速旋转,摩擦副材料需具备摩擦系数小、磨损率低等特点,以提高泵的可靠性和寿命[1]。
国内外研究人员对配流副摩擦磨损特性进行了大量的研究。王正磊等对高转速条件下轴向柱塞泵配流副摩擦磨损特性进行研究,得出与中低转速相比,高转速测试条件下的配流副更容易发生粘着磨损结论[2]。杜玉香等利用表面处理工艺对摩擦副性能进行分析研究,发现38CrMoAl氮化后表面等离子喷涂二硫化钼固体润滑膜与QT500-7(氮化)的配对的磨损量最小且效果最佳[3]。赵存然等采用MMU-10端面摩擦磨损试验机研究了某航空轴向柱塞泵配流副在3#航空煤油介质中的摩擦磨损特性[4]。
可以看出,国内外学者对轴向柱塞泵配流盘摩擦副材料关注度较高,配流盘摩擦副匹配材料的选择对泵的寿命及其可靠性有着非常重要的决定作用。本文开展几组配流副材料的摩擦磨损实验研究具有一定的工程应用价值,为改善配流盘磨损问题提供参考性依据。
针对轴向柱塞泵配流副摩擦特性要求,选用目前几组摩擦特性较好的配对材料进行研究,选用的缸体材料为烧结铜、ZQAL9-4,配流盘材料为25Cr3MoAl、18CrMnTi以及38CrMoAl,组成三对摩擦副。结合缸体与配流盘相互运动关系,加工的上摩擦试件使用缸体材料,下摩擦试件使用配流盘材料,且下试件采用氮化、氮化和渗氮处理。如图1所示,分别为开展实验的上试件和下试件实物照片。摩擦配对情况如表1所示。
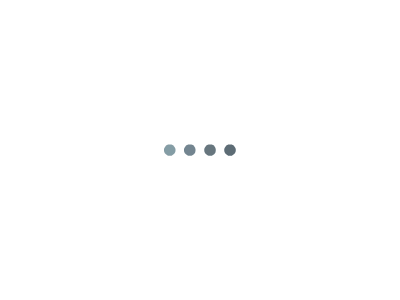
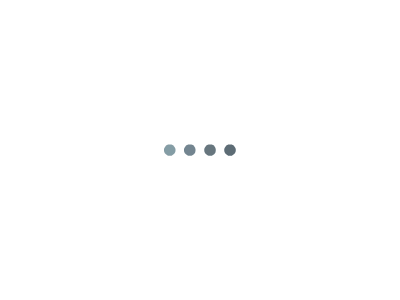
为了完成轴向柱塞泵摩擦副摩擦磨损实验,设计了摩擦磨损实验系统,如图2所示。该系统主要由立式万能摩擦磨损试验机、小型液压站和数据采集计算机三个部分组成。另外准备微精电子天平测量试件质量,每次秤量前,使用超声波清洗机清洗干净[5]。
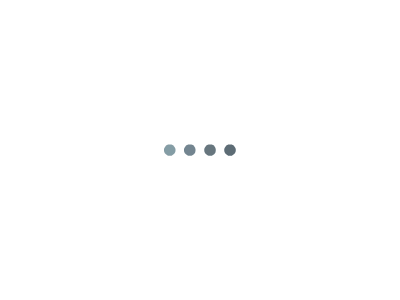
摩擦试验机主轴安装上试件,由电机带动主轴按一定速度旋转,主轴转速通过转速传感器来检测和调整。下试件安装在试验机下侧连接轴上,连接轴上安装有摩擦力矩传感器,用来检测摩擦副之间的摩擦力矩。采集到的主轴转速、试验力和摩擦力矩信息实时传输到数据采集计算机并作处理。
为解决实验过程中温度对实验结果的影响,设计了小型液压站,主要负责摩擦副装置润滑油液的提供和油液的散热,如图2所示。油液自液压站到实验模型中实现循环,进出油口的连接方法采用下入上出方式。一方面利用油液循环流动的特点将摩擦磨损过程产生的大量的热带走,使整个实验过程在温度变化不大的条件下进行,避免上下试件之间发生粘着磨损;另一方面将摩擦磨损过程中产生的磨粒在流动过程中带走,避免上下试件之间发生磨粒磨损。
根据每组摩擦副配对材料实验中得到的摩擦系数数据,绘制出配对材料的摩擦系数变化曲线,最后通过磨损情况和摩擦系数变化情况分析,给出具体的结论,其中平均磨损量的计算利用公式:
在实验前,先对上下试件利用超声波清洗机进行清洗,清洗时放一点除油粉,为了除去试件表面的油污,设置温度为50℃,清洗20min,自然晒干,然后利用微精电子天平进行称重,多次测量求取平均值。在实验时,设置加载力为400N,主轴转速为1500r/min,实验时间为60min,同时启动小型液压泵站使油杯中的油液循环流动。在实验后,取下上下试件,再次利用超声波清洗机对试件进行清洗,与实验前的方法一样,清洗完后进行称重求取平均值。
第一组实验上试件材料为烧结铜,下试件材料为25Cr3MOAl,采集摩擦系数实验数据,绘制其变化曲线如图3所示。
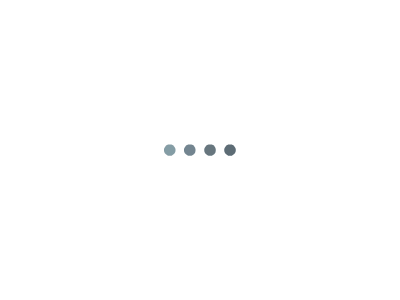
图3 第一组材料摩擦系数曲线
可以得到,该组配对材料的平均摩擦系数值为0.11355,上试件平均磨损量为6.45569×10-6mg/(N•m),磨损量为33.7mg。下试件平均磨损量为-4.41713×10-7mg/(N•m),磨损量为-2.3mg,下试件磨损量为负值的原因是黏附着少许上试件材料。第一组摩擦副材料的总磨损量为31.4mg。
从实验前后试件比对来看,上下试件表面均有轻微的刮擦磨损,下试件磨损量为负值且很小,考虑到微精电子天平精度的情况,此时下试件应该有一个非常小的磨损量,且磨损量值接近于零。相对下试件,上试件的磨损量较大。由实验摩擦系数曲线图得出,若单从摩擦系数方面来看,摩擦副在对磨时摩擦系数不稳定,上下波动较大。
第二组实验上试件材料烧结铜,下试件材料为38CrMoAl,经过实验所获得如图4所示的摩擦系数变化曲线。
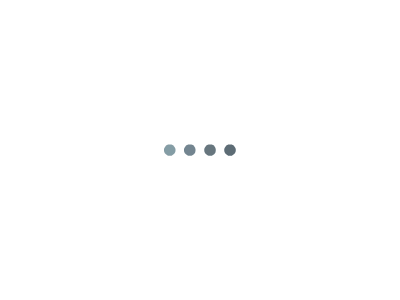
可以得到,该组配对材料的平均摩擦系数值为0.06646,上试件平均磨损量为3.82630×10-7mg/(N•m),磨损量为2.0mg。下试件平均磨损量为5.77066×10-8mg/(N•m),磨损量为0.3mg。第二组摩擦副材料的总磨损量为2.3mg。
从实验前后试件对比,很明显可以看出,上下试件表面只产生细微的刮擦磨损,上下试件磨损量值都很小,考虑到微精电子天平精度的情况,同样下试件磨损量几乎接近于零。由实验摩擦系数曲线可以看出,摩擦副对磨时摩擦系数基本保持一个降低的趋势,在大约3000 s时,突然有了一次增大后又继续呈现降低趋势。综合上下试件的磨损量和摩擦系数曲线图来看,该对摩擦副的摩擦磨损性能较好,适合配对摩擦副的材料选型。
第三组实验上试件材料为ZQAl9-4,下试件材料为18CrMnTi,经过实验所获取的摩擦系数变化曲线如图5所示。
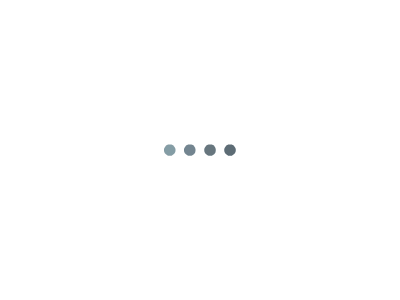
该对材料摩擦副的平均摩擦系数值为0.04094,上试件平均磨损量为9.16594×10-6mg/(N•m),磨损量为48.0mg。下试件平均磨损量为-1.34610×10-7mg/(N•m),磨损量为-0.7mg。摩擦副的总磨损量为47.3 mg。
此时上下试件表面只产生轻微的刮擦磨损,下试件磨损量值为负,且负值很小,此时下试件应该处于一个非常小的磨损情况,磨损量值可能接近于零。摩擦副对磨时摩擦系数基本保持一个降低的趋势,且波动幅度不是太大,综合上下试件的轻微刮擦以及下试件超低的磨损量和稳定的摩擦系数,该对摩擦副也较适合配对摩擦副的材料选型。
综合以上三组实验磨损量数值,分别画出上、下试件的磨损量分布图如图6所示,上下试件磨损量之和即为摩擦副的总磨损量。
从图6可以看出这三组配流盘摩擦副配对材料中,第二组实验即烧结铜和38CrMoAl的配对材料具有最小的磨损量和较低的摩擦系数,也就意味着该对材料制作的轴向柱塞泵配流盘摩擦副具有最优的摩擦磨损特性。
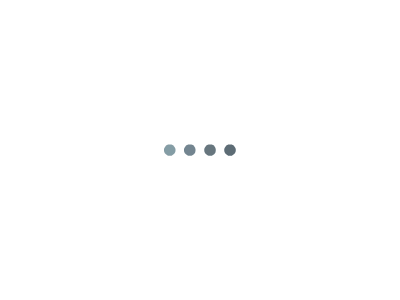
综上所述, 对某型号的轴向柱塞泵缸体材料采用烧结铜,配流盘材料为氮化处理的38CrMoAl时,摩擦副对磨时摩擦系数基本保持一个降低的趋势, 且上下试件的磨损量也最小,因此具有最优的摩擦磨损性能。研究结论为配流盘摩擦副材料选择提供一定的参考。
参考文献
[1] 马纪明,黄怡鸿,郭健,等.液压柱塞泵运动副磨损特性研究综述[J].液压与气动,2017,(8):84-94.
[2] 王正磊,吴玉程,黄家海.高转速条件下轴向柱塞泵配流副摩擦磨损特性[J].液压与气动,2019,(8):27-32.
[3] 杜玉香,马利云,王耀华.表面处理工艺对摩擦副性能的分析研究[J].液压气动与密封,2013,33(7):66-68.
[4] 赵存然,姜继海.航空煤油轴向柱塞泵用配流副材料磨损特性研究[C]//中国机械工程学会流体传动与控制分会.第九届全国流体传动与控制学术会议(9th FPTC-2016)论文集.杭州:中国机械工程学会流体传动与控制分会,2016:425-429.
[5] 李少年,林凯,刘浩.转速对叶片泵配流盘摩擦副摩擦特性的影响[J].液压气动与密封,2019,39(1):53-55.
原文始发于微信公众号(液压气动与密封):轴向柱塞泵配流盘摩擦副材料的磨损实验研究
本文来自液压气动与密封,本文观点不代表iHydrostatics静液压立场。