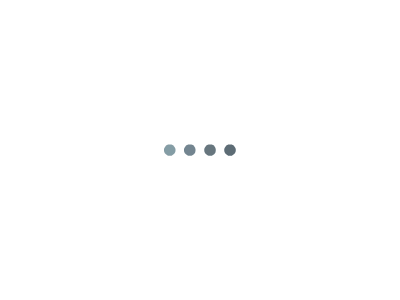
选择缸径有五个设计标准:
• 满足超速要求,这适用于压力机和类似机器。
• 杆径必须足够大,以避免因杆长度和负载而发生弯曲。
• 固有频率必须比加速度频率高2 至100 倍,具体取决于所需的跟随误差、阻尼系数和所使用的控制算法。
• 必须有足够的力来加速伸出和缩回方向上的负载。
• 减速时必须防止气蚀(流体中形成气泡)。通常,这种情况仅出现伸出重负载,然后试图快速减速时发生,称为超速负载。
前两个标准非常简单。标准一很容易计算,标准二需要查找液压缸制造商的说明书来检查杆径是否足够大。然而,标准三取决于电子控制器所使用的控制算法。这里就是液压运动控制器可以物有所值的地方。简单的PLC控制可以仅使用比例增益。系统的固有频率需要非常高才能获得合适的响应。不幸的是,将固有频率增加两倍需要将缸径增加大约相同的量,但流量要求增加四倍。这可能导致液压系统设计很昂贵。具有 PID 、速度以及加速度前馈 (FF) 的液压运动控制器需要的固有频率约为加速度频率的四倍。最好的液压伺服运动控制器可以允许固有频率降低到加速度频率的大约两倍。只要满足上述其他标准,能够在同一应用中使用较小直径的液压缸可以节省大量资金。
该图显示了运动曲线中关键速度和力发生的位置。两个 VCCM 方程需要这四个值来计算液压缸工作端的面积Ape
标准四很难计算。通常,加速负载时需要最大的力。假设运动控制器在斜坡时使用 S 曲线,则峰值加速度出现在最大稳态速度的一半处。这意味着将供油压力乘以活塞面积,然后除以质量,将不会得到有效的答案。原因是当油流经伺服阀到达活塞的工作端时会发生压力损失。此外,背压作用在活塞的回油侧,将油排出液压缸。这意味着在不进行数学计算的情况下,活塞的工作侧和回油侧的压力是未知的。可以计算力的差值并用于计算所需稳态速度一半时的潜在加速度。
必须满足标准五,以避免减速时出现气蚀。当尝试垂直负载减速或必须快速减速时,超速负载引起的气蚀是常见的。气蚀通常只是液压缸盖端的问题。计算此值需要知道从最大稳态速度减速而不导致液压缸盖端压力变为零所需的制动力。
计算固有频率
使用几个不同的公式来计算固有频率。如下为其中一个:
需要注意的是保持单位正确。固有频率的单位为弧度每秒。要将弧度每秒转换为赫兹,请除以 2π。
固有频率(以Hz为单位)必须与加速度频率进行比较。缸径必须增大,直到固有频率是加速度频率的四倍。这是基于PID算法将与前馈一起使用的假设。我使用一个计算机程序,该程序将从最小到最大列出液压缸尺寸表,直到满足固有频率要求。
VCCM(探索液压伺服运动控制中的VCCM方程或VCCM-如果流量计算不再是Q=A*V?)方程还可用于计算缸径和伺服阀阀规格。需要两个 VCCM 方程来计算缸径和伺服阀规格。VCCM 方程为:
然而,该方程假设伺服阀完全打开。最好留一些余地,所以我将 Kvpl 乘以 0.9。假设当阀打开 90%(而不是 100% 打开)时,活塞达到所需的最大稳态速度:
第二个方程与第一个方程相同,但有一些修改。该速度是峰值加速度出现时所需的最大稳态速度的一半。在半速(峰值加速度)下,阀打开60%。60%值来自以下事实:在最大稳态速度一半的情况下,由于速度前馈,阀应打开约45%。剩余的15% 是峰值加速度时加速度前馈的估计值。第二个 VCCM 方程使用摩擦力加上以峰值加速度加速负载所需的力:
现在我们有两个方程和两个未知数,即伺服阀工作端的流量常数 Kvpl 和液压缸工作端的面积Ape。事实上,有四个未知数。阀芯面积比和液压缸两腔有效工作面积比也未知。求解这两个未知数需要一点数学知识。油缸工作端面积的求解相对容易,但伺服阀工作端流量常数的求解则不然。幸运的是,油缸工作端面积的解不依赖于液压缸比或伺服阀 A 口和 B 口的流量常数之比。Ape 的公式为:
假设 v1 是 v2 的一半。
如果液压缸的活塞杆朝下(如在液压机中),则活塞工作端的面积可能为负。当重力足以使杆延伸时,就会发生这种情况。在这种情况下,将使用相同的公式但使用缩回值来确定缸径。
伺服阀流量常数的公式非常复杂,所以我们暂时忽略它。原因是计算伺服阀规格的公式假定液压缸工作端面积的解是将用于计算阀流量常数的值。该公式是准确的,但尝试找到一个具有与计算出的活塞面积完全相同的液压缸,Ape!因此,下一步是搜索标准油缸规格表,找到满足面积要求的下一个最大直径。
我通常首先找到活塞盖端侧的面积。一旦我发现,杆直径有两种选择。标准杆尺寸导致杆端面积约为盖端面积的70%。还有一种杆直径选项,杆端的面积为盖端的50%。我通常从标准尺寸的杆直径开始。现在液压缸比已知。此时阀芯比假定为 1。
下一步是使用 Kvpl 方程的公式(使用更新后的工作端四舍五入面积)来计算阀流量常数:
接下来,可以计算阀规格。假设阀的额定压力为 70 bar,则每个通道的压降将为 35 bar,因此:
解决方案应尝试标准比例和2:1比例液压缸尺寸以及标准对称和非对称阀芯。有时,非对称阀芯对于减速时可能产生气蚀的系统效果会更好。如果液压缸杆向上推,则使用活塞面积比为 2:1 的液压缸效果更好。
现在必须检查设计是否存在气蚀,以满足标准五。计算液压缸和负载是否会产生气蚀将在另外的文章中介绍(使用 VCCM公式检查油缸气蚀或利用VCCM方程解决液压缸的汽蚀问题)。
原文始发于微信公众号(液压传动与控制):液压伺服系统设计:液压缸和伺服阀选择
原创文章,作者:iHydrostatics静液压,如若转载,请注明出处:https://www.ihydrostatics.com