昨天,我们简要介绍了电动执行机构的结构和工作原理。
今天,我们将全面分析油缸和电缸的优缺点,探讨油缸是否会被电缸取代。这究竟是杞人忧天,还是不可避免的趋势呢?让我们一同深入探讨。
先提醒一下,我们明晚8点(6月13日周四)邀请汤姆森的陈经理来为大家做一场关于电动推杆选型的讲座,大家如果需要观看回放的话,需要先扫码登记哦!
扫码后,可观看回放!
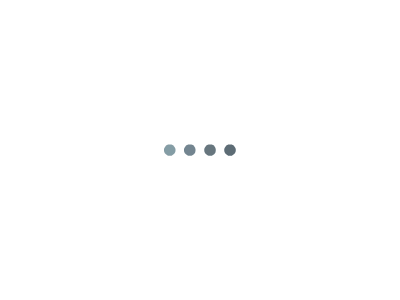
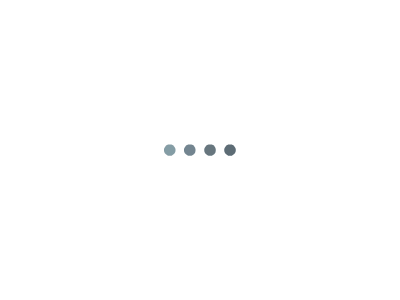
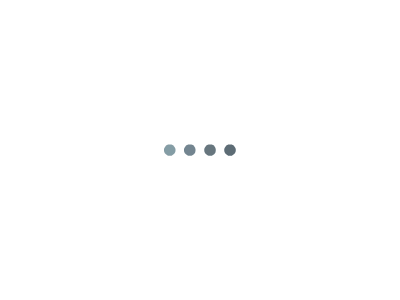
培训大纲如下:
液压缸相较于电缸的明显优势
1
驱动力大,适合重载应用
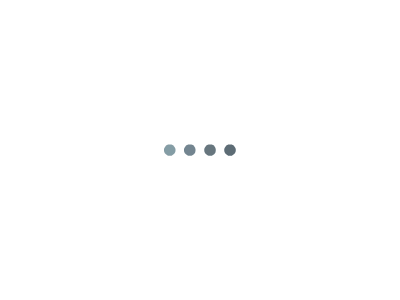
这也是绝大部分液压从业人员用来否定电缸不行的唯一理由。
该理由,目前来说,是成立的。确实在重载工况,以汤姆森的电动推杆为例,目前最大负载力为25000N(2.5T),超过了就没有标准产品可用了。
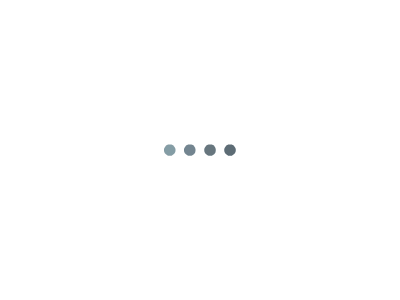
但并不是说,电驱就不能超过2.5T,本人用过的采用伺服电机驱动增压器的方案,可驱动的负载达到10T,但这属于非标定制产品,不作数!
2
速度和负载大小无关
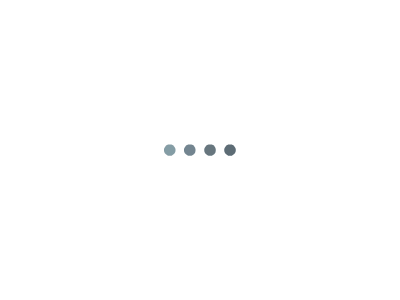
液压缸的运动速度和负载大小无关,我们知道,液压系统中,液压缸的运动速度取决于泵的输出流量,所以不受负载大小的影响。
而一般来说,电动推杆却不行,因为电动推杆由电机直接驱动的,而电机的特性是输出扭矩与电机转速成反比。因此,如果你需要驱动重载运行,必然会牺牲一定的运动速度。在电动推杆内部,正是通过一对减速齿轮来实现“降速增扭”的效果。
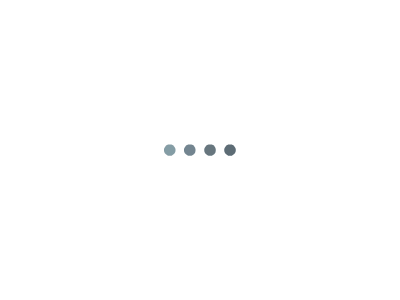
当然了,随着技术的发展,汤姆森最新开发的XD系列电动推杆,已经可以做到负载在特定范围内变化时,速度并不会发生变化,当负载增加时,只要增加电流就可以了。所以这一条优势,可能就不存在了。
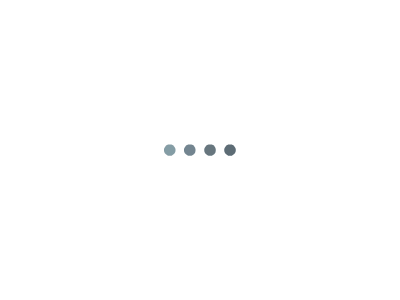
3
可以承受较高的负载冲击力
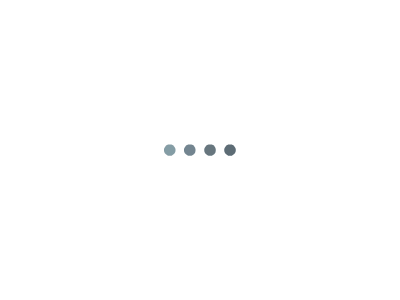
液压缸内部流动的是液压油,遇到外部冲击载荷是,是有一定缓冲作用的。液压油实际可以想象成“液体弹簧”。
而电缸则是由丝杆硬碰硬的来驱动负载的,一旦外部冲击载荷过大,直接丝杠损坏,没什么缓冲余地。
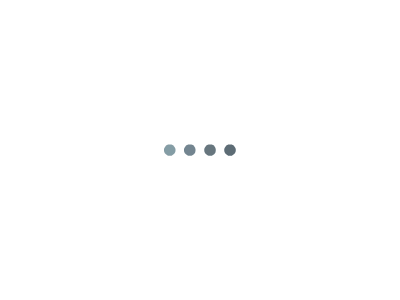
当然了,随着技术的发展,电缸也在采用一些措施来吸收一部分冲击,如下图所示,增加了一组减震垫圈。缓冲效果如何,还有待验证,但至少已经推出了解决方案。
所以这一条优势,可能就不存在了。
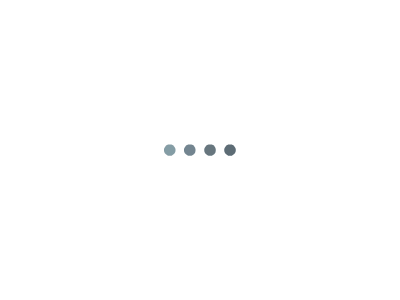
电缸相较于液压缸的明显优势
1
设计和结构布局都很简单
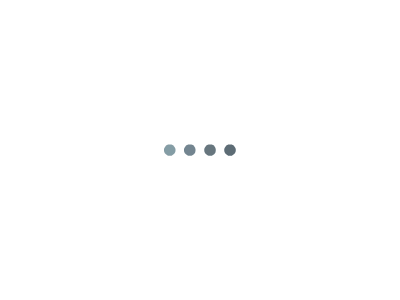
采用电缸/电动推杆,需要接的就是电缆线;不像液压系统,哪怕只有一根液压缸,那么从液压泵、电机、安全阀、换向阀、节流阀,各种接头、高压过滤器、回油过滤器,蓄能器、传感器等等一堆东西组成的液压泵站,额外还有两根永远少不掉的液压软管/硬管。
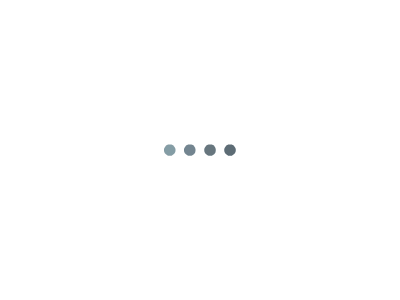
2
效率高、不受温度变化的影响
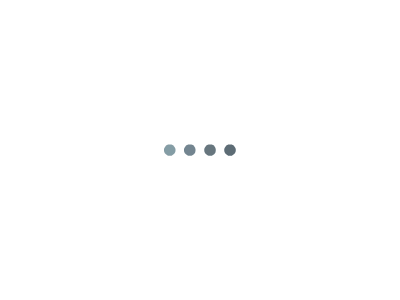
电动缸或电动推杆实际为机械传动,其能量损失仅为机械摩擦损失。而反观液压系统,除了机械损失外,还有系统的节流损失、溢流损失,各类液压元件的内泄漏、外泄漏损失。而且随着油液温度的升高,损失更高,控制精度更差。
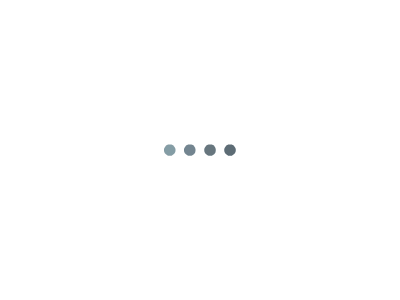
3
寿命期内,免维护
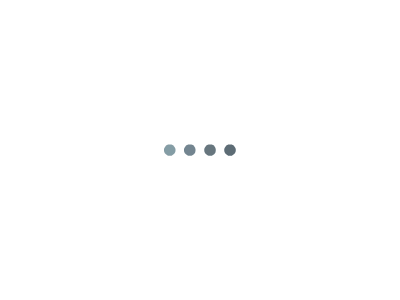
正如我们在上一讲分析电动缸/电动推杆的结构时所看到的,整个系统的零部件数量相当少,因此经过特殊设计,在设计生命周期内(5~10万次,根据负载和运动行程有所不同,实际就是滚珠丝杠的寿命),可以实现免维护!
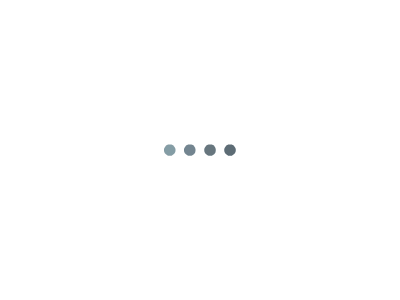
然而,对比之下,液压系统在刚启动新设备时就可能出现损坏的情况并不少见。在使用过程中,不仅需要监测油温和油液污染情况,还需检查是否存在外部泄漏,并防止外部污染物的侵入。此外,液压元件的密封件也需要定期更换。
4
控制精度高,有严格的传动比
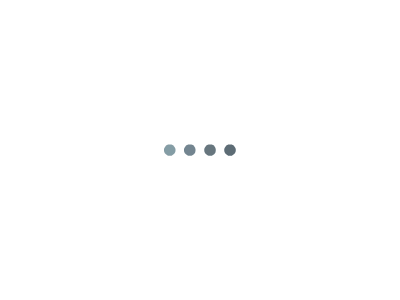
还是得益于电机直接驱动滚珠丝杠的结构设计,我们知道滚珠丝杠的加工精度非常高,所以最终获得的传动精度也非常高。此外,系统中安装了减速器,具有固定的传动比,从而实现精确控制。
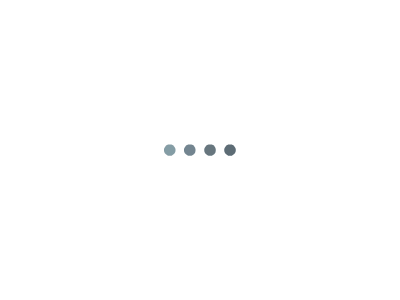
5
可控性、智能化程度高
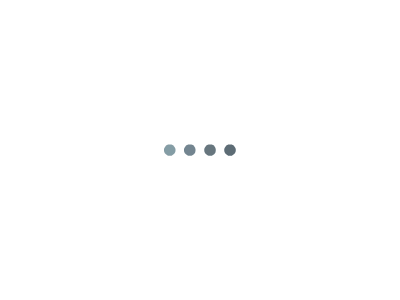
可以通过定位器、编码器、控制板卡来实现多样化的动作控制,故障监测与诊断。而液压系统要实现这些功能,那要配置的东西可就多了,各种流量、压力控制阀、外部压力和流量传感器、位置传感器等等。
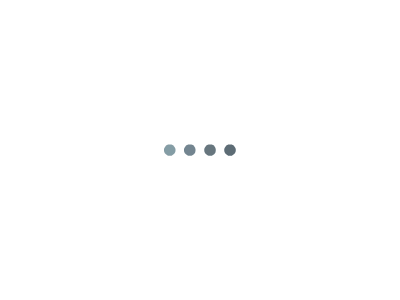
6
高度节能
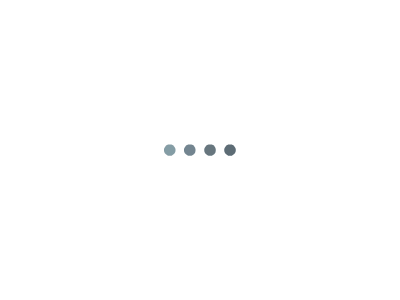
电机直接驱动,当不需要动作时,电机可以停止运行。相比之下,无论液压系统处于何种工况,只要系统在工作,液压泵都必须保持运行状态,即使在保压工况下也是如此,以确保液压系统的快速响应。即便采取了一些节能措施,液压系统中的电机依然无法完全停止运行。因此,与液压系统相比,电动缸的节能效果变得尤为显著。
写完这篇文章,突然想转行!
我怎么感觉被我这么一写,液压变得全部都是劣势了,仅有的一些优势也逐渐在被电缸的发展所破解了。完了,我是不是该转行了!
原文始发于微信公众号(液压贼船):你认为油缸无法被电缸取代的那些优势,现在还有几个成立的?
原创文章,作者:iHydrostatics静液压,如若转载,请注明出处:https://www.ihydrostatics.com
评论列表(1条)
液压缸能输出兆瓦级功率,电动机虽然可以,但减速机、丝杆做这么大,不仅频响精度差,重量和成本都远远高于液压了。知己知彼、各尽所长,才是工业系统设计的关键。